Porosity in Welding: Identifying Common Issues and Implementing Best Practices for Avoidance
Porosity in welding is a pervasive issue that usually goes unnoticed till it triggers significant troubles with the integrity of welds. This usual flaw can compromise the toughness and toughness of welded frameworks, posing security threats and causing pricey rework. By understanding the origin causes of porosity and carrying out effective avoidance strategies, welders can substantially enhance the top quality and integrity of their welds. In this discussion, we will check out the crucial aspects adding to porosity development, examine its harmful results on weld efficiency, and go over the most effective techniques that can be embraced to reduce porosity occurrence in welding processes.
Usual Reasons of Porosity
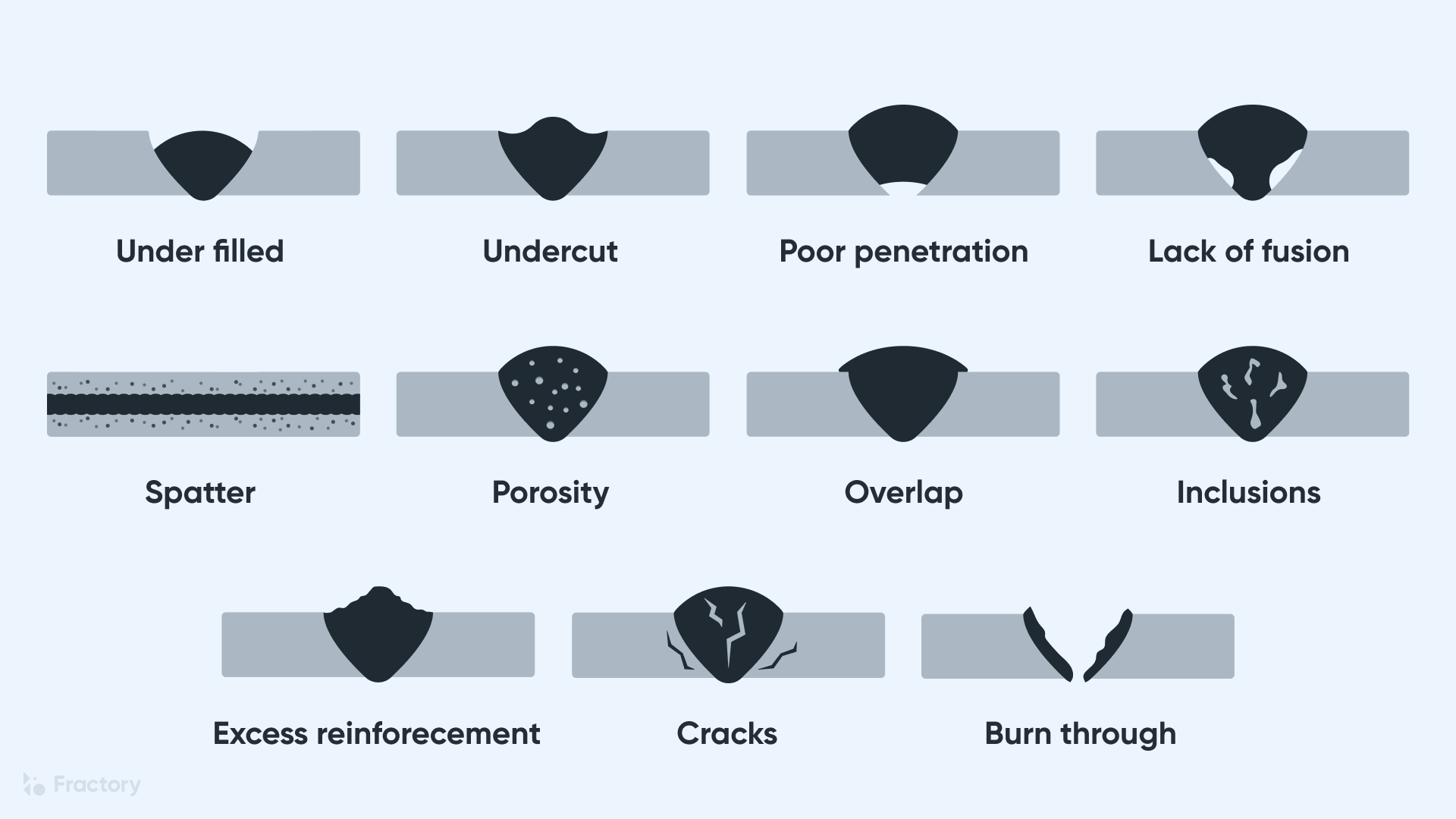
Using dirty or wet filler materials can introduce impurities into the weld, contributing to porosity issues. To mitigate these common reasons of porosity, thorough cleaning of base steels, correct securing gas selection, and adherence to optimal welding parameters are important practices in achieving high-quality, porosity-free welds.
Impact of Porosity on Weld Top Quality

The visibility of porosity in welding can significantly endanger the architectural stability and mechanical residential properties of welded joints. Porosity creates gaps within the weld steel, compromising its overall toughness and load-bearing capability. These voids act as stress and anxiety concentration points, making the weld extra prone to cracking and failure under used tons. Additionally, porosity can lower the weld's resistance to rust and other ecological elements, further reducing its longevity and efficiency.
Welds with high porosity degrees tend to exhibit lower impact strength and decreased capability to warp plastically before fracturing. Porosity can hinder the weld's capability to efficiently transfer forces, leading to premature weld failure and potential safety hazards in crucial structures.
Best Practices for Porosity Prevention
To enhance the architectural integrity and quality of welded joints, what certain steps can be carried out to reduce the occurrence of porosity throughout the welding process? Making use of the correct welding strategy for the details product being bonded, such click site as changing the welding angle and weapon setting, can better protect against porosity. Normal evaluation of welds and prompt removal of any kind of problems recognized throughout the welding process are essential techniques to avoid porosity and generate premium welds.
Significance of Correct Welding Strategies
Implementing proper welding techniques is paramount in guaranteeing the architectural honesty and top quality of bonded joints, building on the structure of try this effective porosity prevention steps. Welding techniques straight impact the overall stamina and resilience of the welded framework. One key element of appropriate welding strategies is maintaining the right warmth input. Too much warmth can lead to boosted porosity as a result of the entrapment of gases in the weld pool. Conversely, insufficient warmth might result in insufficient fusion, creating potential weak points in the joint. Furthermore, utilizing the proper welding parameters, such as voltage, current, and travel speed, is crucial for accomplishing audio welds with very little porosity.
In addition, the option of welding process, whether it be MIG, TIG, or stick welding, ought to align with the specific demands of the project to make sure optimal results. Correct cleaning and preparation of the base metal, along with selecting the best filler material, are also necessary components of proficient welding techniques. By sticking to these best practices, welders can lessen the threat of porosity formation and generate high-quality, structurally audio welds.

Examining and Quality Assurance Procedures
Quality assurance actions play a crucial function in validating the honesty and integrity of bonded joints. Checking procedures are vital to discover and stop porosity in welding, ensuring the stamina and sturdiness of the end product. Non-destructive screening approaches such as ultrasonic testing, radiographic testing, and check these guys out visual evaluation are typically employed to determine possible defects like porosity. These methods allow for the evaluation of weld top quality without jeopardizing the integrity of the joint. What is Porosity.
Post-weld examinations, on the other hand, analyze the last weld for any kind of issues, including porosity, and confirm that it meets specified standards. Executing an extensive high quality control strategy that includes extensive testing procedures and inspections is paramount to reducing porosity concerns and making certain the total high quality of welded joints.
Verdict
To conclude, porosity in welding can be an usual problem that impacts the high quality of welds. By recognizing the usual reasons for porosity and carrying out best techniques for avoidance, such as proper welding strategies and screening procedures, welders can ensure premium quality and trustworthy welds. It is necessary to prioritize avoidance methods to decrease the event of porosity and keep the honesty of welded structures.